Production site
WHERE INNOVATION TAKES SHAPE
Quality is also demonstrated through a production process that takes place entirely within SAFE, using raw materials made in Italy and combining manual skill and technology. A painstaking process with a craftsman’s approach, combining manual skills and highly specialised training.
13.057 m²
Total surface area
1,692 m²
Offices and SVC
550 m²
Production department
4,486 m²
Warehouse
5,489 m²
Assembly and testing
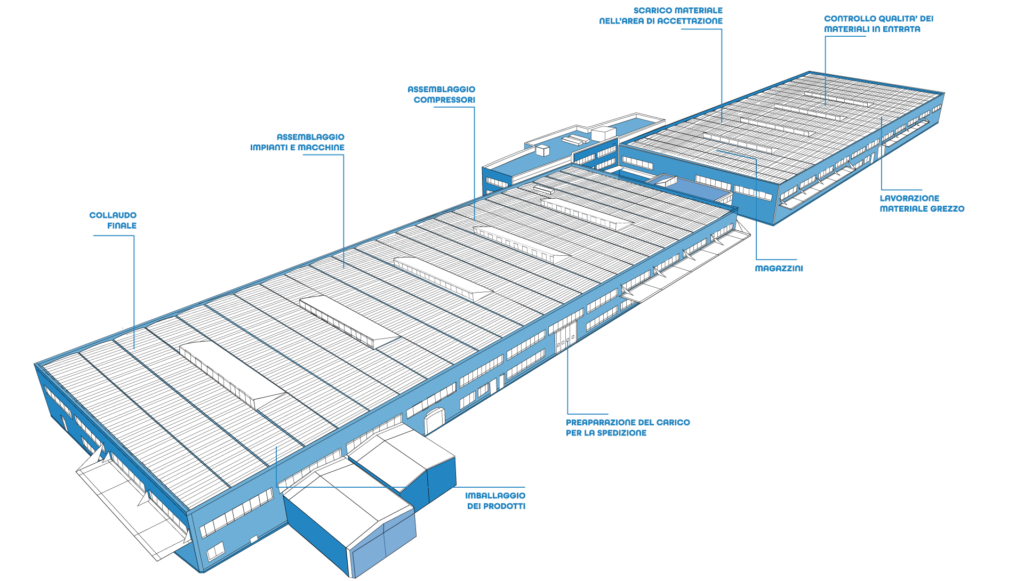
MATERIAL ACCEPTANCE AND STORAGE
The designated personnel verify the products and accompanying documentation by identifying the material, and by carrying out the checks specified by internal procedures. During acceptance the components are subjected to testing according to the quality control procedure. The material is stored in designated areas and vertical warehouses according to the type of product, while awaiting shipment to the Customer or use in production.
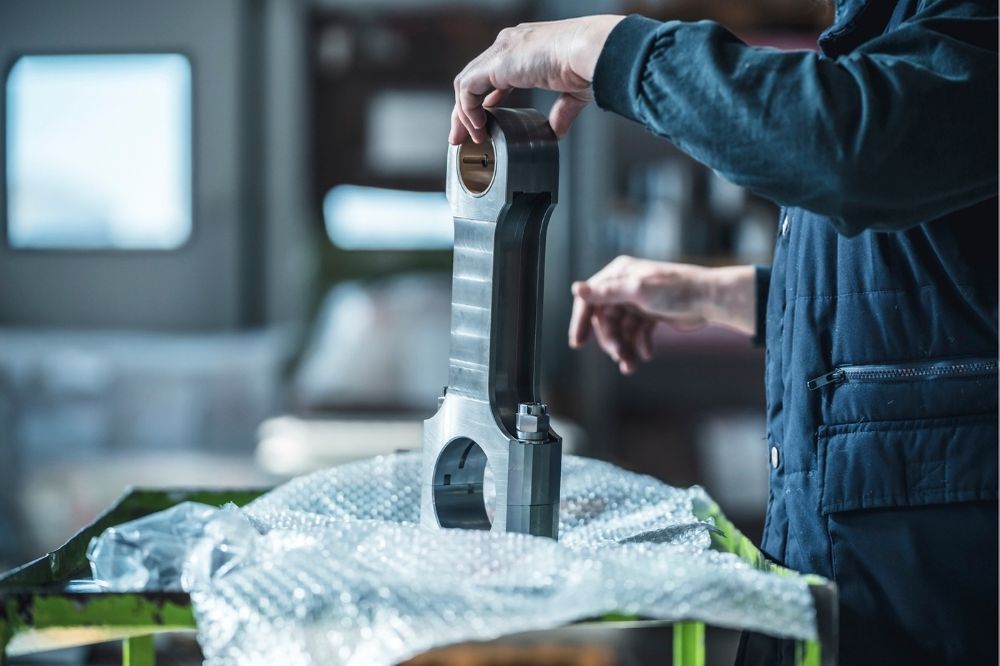
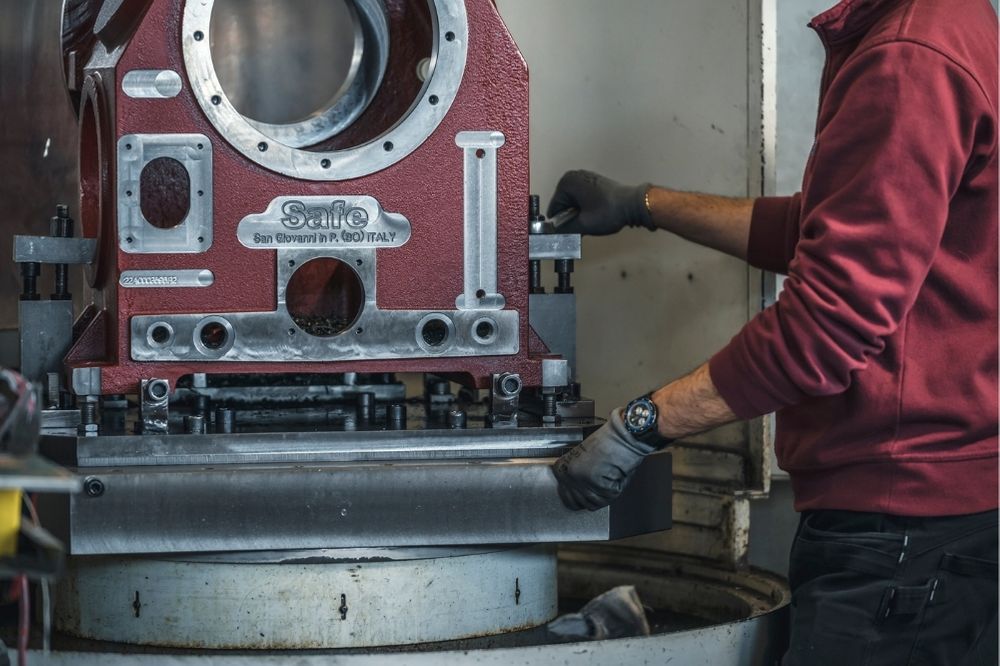
CUTTING OF RAW MATERIAL AND MECHANICAL MACHINING
Raw materials are cut according to the dimensions required for machining on machine tools. This is followed by turning and milling carried out by innovative machinery.
COMPRESSOR ASSEMBLY
Assembly of the compressor and the entire system is carried out by SAFE’s technical experts in according to the design, based on the bill of materials, diagrams and relevant specifications.
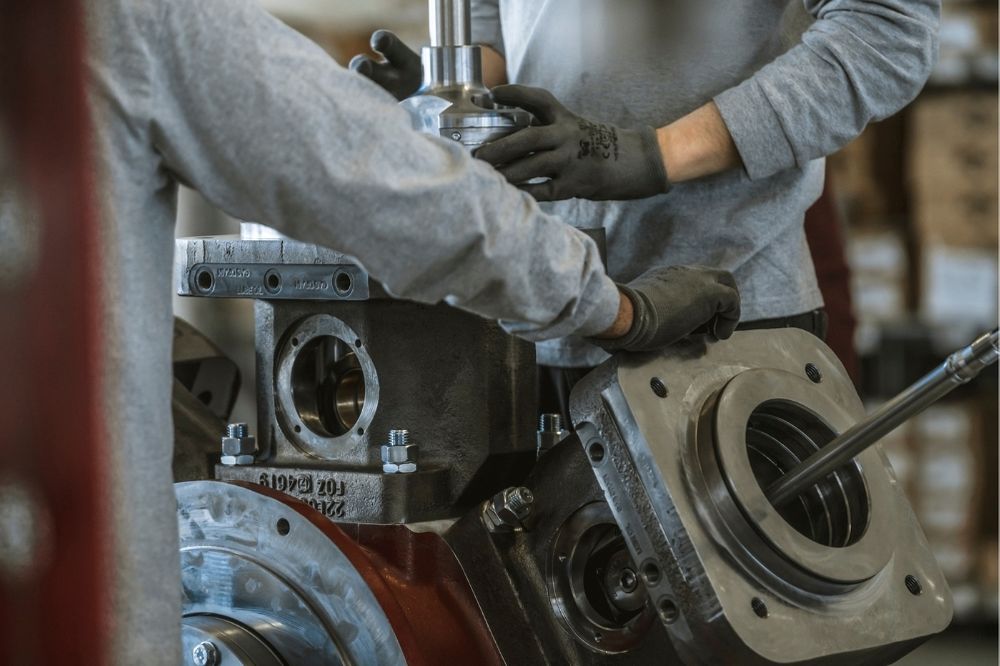
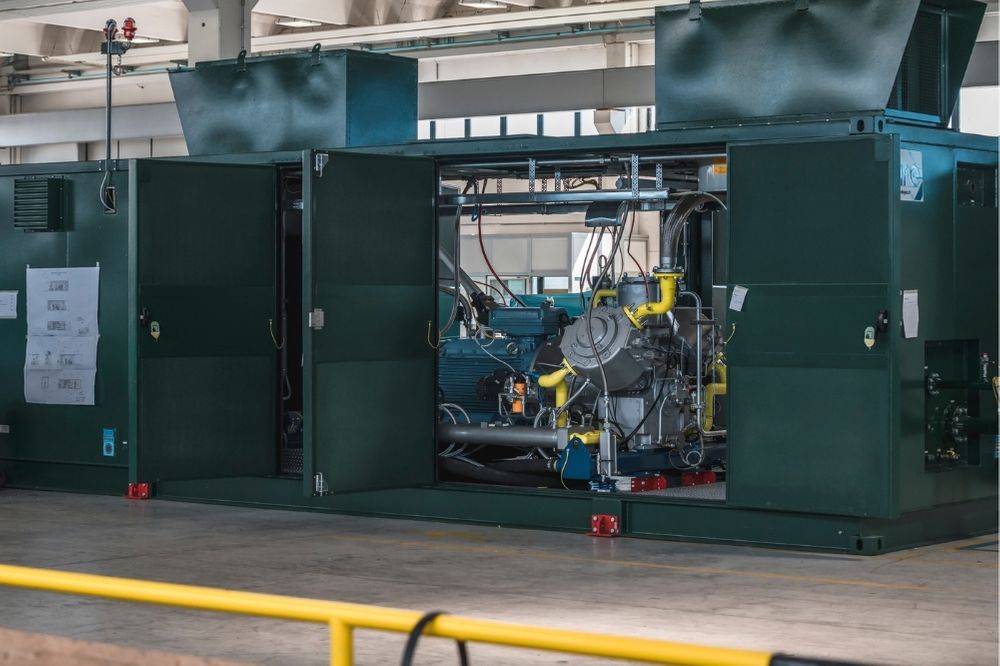
CORE UNIT ASSEMBLY
The heart of the system is the compressor, which can be placed inside a cabinet if required by the Customer’s specifications. The entire structure is designed to reduce noise pollution and is painted with special low environmental impact requirements.
SYSTEM ASSEMBLY
Other equipment such as cylinder packs, dispensers, air coolers or dryers can be added to the system. All of them are made in SAFE and designed to rationalise spaces.
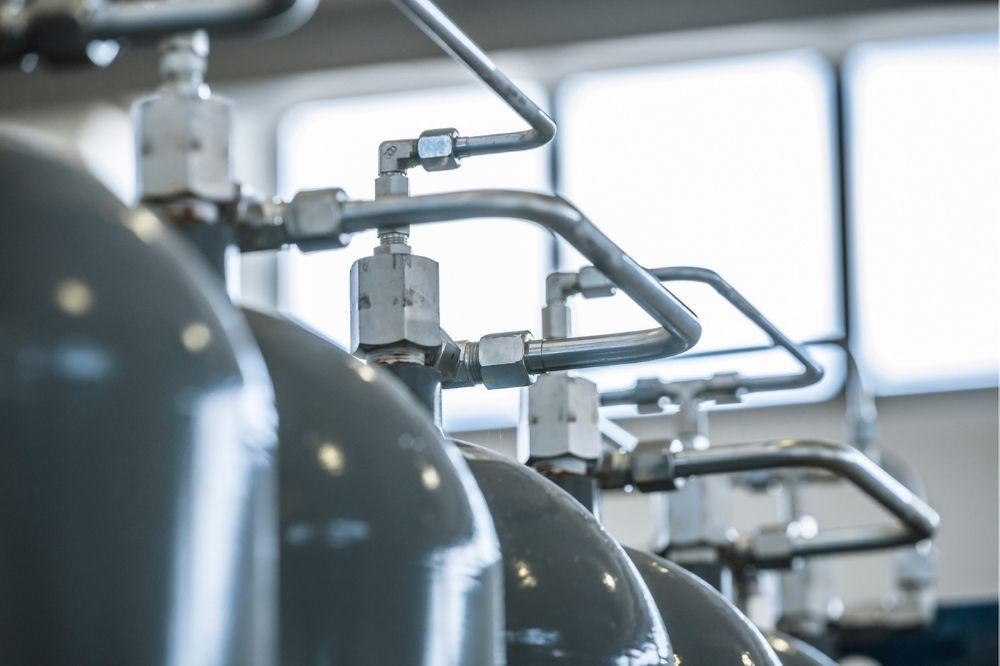
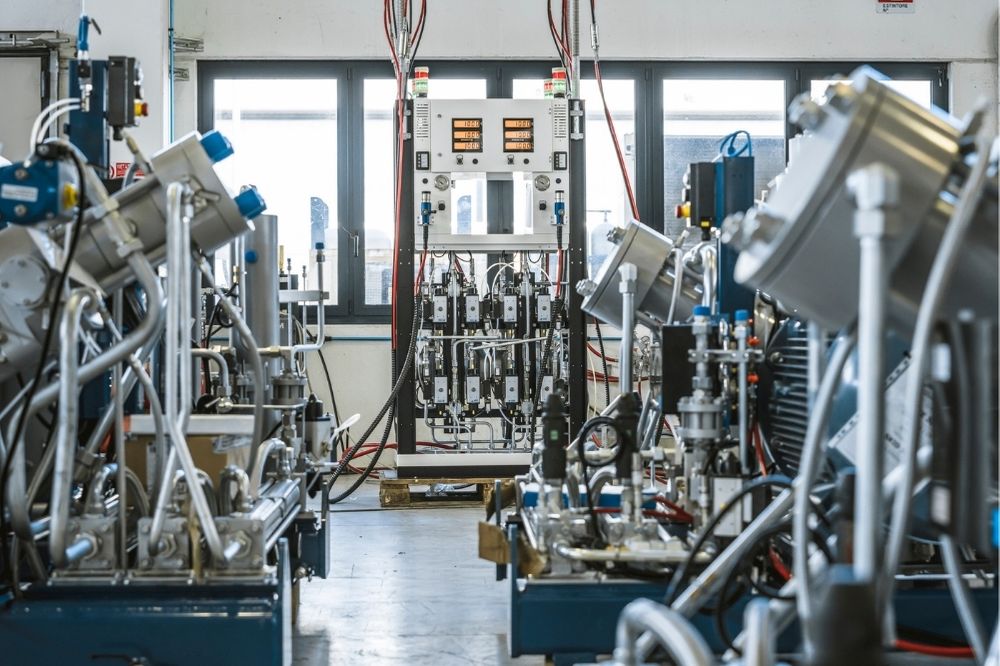
FINAL TESTING
At the end of the assembly activity, the system performs a functional and leakage test in full compliance with safety regulations in a designated area. The dispensers are also tested to check that they are working properly and calibrated perfectly. At the end of the operations, a report is compiled containing the system data, the performance and the result of the testing.
PACKAGING AND SHIPPING
The products to be shipped are carefully packed and protected to ensure integrity and safety, and to avoid damage during transport. The solution is then loaded using special equipment and sent to the Customer, together with all the corresponding documentation.
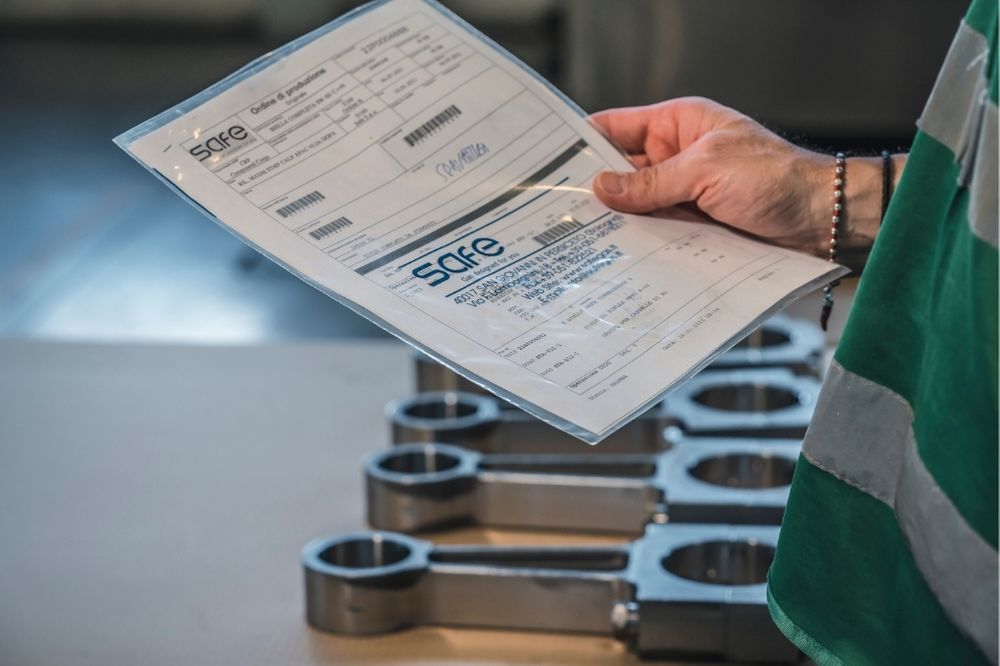
SAFE’S SPECIALITY: QUALITY CONTROL
Quality control is the cornerstone of the entire production chain: from the arrival of materials, to their processing, and right up to the assembly and testing of the entire solution. Starting from the acceptance of raw materials, the documentation is checked and subjected to control. If the check on compliance with SAFE specifications is negative, the material can be rejected and returned to the supplier or reworked. The finished products undergo a series of checks to ensure the correct manufacture and functionality of each component. Subsequently, all solutions are trialled and tested before being sent to the Customer. Testing normally lasts 4 hours and takes place in a special area with 4 sections, all complying with safety standards according to three risk factors: gas, pressure and electricity. The large area supplied makes it possible to:
Reduce
delivery times
Increase production capacity
Reduce risks related to safety
Increase product reliability and performance